October 30, 2017
In fiscal 2017 Greening Excellent Plant, Etc., Commendation, Suntory’s two plants won the
“Kanto Bureau of Economy, Trade and Industry Director's Award” and the “Japan Greenery Research and Development Center Chairman's Award.”
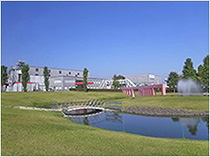
Suntory Products Limited
Haruna Plant
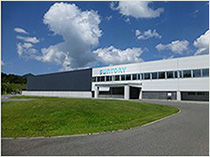
Suntory Products Limited
Okudaisen Buna no Mori Water Plant
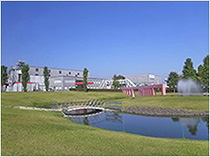
Suntory Products Limited
Haruna Plant
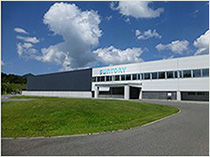
Suntory Products Limited
Okudaisen Buna no Mori Water Plant
At the fiscal 2017 Greening Excellent Plant, Etc., Commendation, the Haruna Plant (located in Gunma Prefecture) of Suntory Products Limited won the Kanto Bureau of Economy, Trade and Industry Director's Award. Also, the Okudaisen Buna no Mori Water Plant (located in Tottori Prefecture) of Suntory Products Limited won the Japan Greenery Research and Development Center Chairman's Award. These awards are presented to factories, etc., that have actively promoted greening and have made outstanding contributions to improving the environment inside and outside of the factory. The awards ceremony for the former will be held from 2:00 PM on November 6 (Monday) at the Kanto Bureau of Economy, Trade and Industry (Saitama City, Saitama Prefecture). The ceremony for the latter will be held from 2:00 PM on November 1 (Wednesday) at Ishigaki Memorial Hall (Minato Ward, Tokyo).
As a company supported by nature's gifts, Suntory Beverage & Food Limited recognizes our responsibility for preserving and regenerating nature and reducing environmental impact. With that in mind, we have set Targets toward 2020*1 based on the Environmental Vision toward 2050 established by the Suntory Group for contributing to the creation of a sustainable society, and are conducting various activities aimed at reducing environmental impact. Each plant conducts greening initiatives on its premises in order to promote coexistence with nature and the community. Plants also conduct activities for saving energy, saving water, reducing the weight of containers and packaging, etc.
*1
(1) 42% reduction in water used for the washing and cooling of manufacturing facilities and containers at Suntory plants *2
(2) 25% reduction in CO2 emissions*2 within our value chain as a result of the further weight reduction of containers, the utilization of renewable raw ingredients and bio-based materials, the active introduction of vending machines consuming the lowest amount of power in Japan, etc.
*2
Reduction in terms of intensity based on the assumption of 2007 business domains
The Haruna Plant of Suntory Products Limited has a beloved garden symbolized by an elm tree. Furthermore, the plant strives to efficiently utilize energy via a cogeneration system*.
The Okudaisen Buna no Mori Water Plant of Suntory Products Limited plants trees in harmony with naturally-growing trees (beech) in the surrounding mountains. The plant also stores snowfall from the surrounding area. The snow is used in a snow chamber and thermal storage system air conditioning and cooling of facilities. The plants have designated their water source areas as the Natural Water Sanctuary Akagi, Natural Water Sanctuary Komochiyama, and Natural Water Sanctuary Okudaisen. Through these sanctuaries, the plants work to cultivate water resources and protect biodiversity.
* Cogeneration system. A system that extracts multiple forms of energy (electricity, heat, etc.) from a single fuel source.
Based on the Suntory Group’s shared corporate message of Mizu to Ikiru (living with water), Suntory Beverage & Food Limited holds a variety of activities related to water. Examples include protection and regeneration of the natural environment, reduction of environment impact, and environmental education focusing on water for younger generations.
In January 2017, in response to how the Suntory Group is expanding its corporate activities globally, the Suntory Group Sustainable Water Philosophy was formulated as basic philosophy for all its water related activities. Moving forward, the over 300 Group companies in Japan and abroad will share this philosophy while conducting activities for the preservation of water, the most important resource for the company’s business, in accordance with the individual environment of each region.
October 31, 2014
Haruna Plant, Suntory Products Limited
Japan Greenery Research and Development Center Chairman's Award at the 33rd National Convention for the Promotion of Factory Greening
Held by the Japan Greenery Research and Development Center
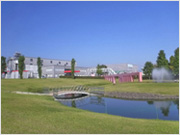
The Haruna Plant of Suntory Products Limited won the Japan Greenery Research and Development Center Chairman's Award at the 33rd National Convention for the Promotion of Factory Greening This award is presented to factories, etc., that have actively promoted greening and have made outstanding contributions to improving the environment inside and outside of the factory. The Haruna Plant Limited has a beloved garden symbolized by an elm tree. Furthermore, the plant strives to efficiently utilize energy via a cogeneration system*.
* Cogeneration system. A system that extracts multiple forms of energy (electricity, heat, etc.) from a single fuel source.
June 1, 2009
Okudaisen Buna no Mori Water Plant, Suntory Products Limited was selected for the New Energy Top 100
Jointly held by the Ministry of Economy, Trade, and Industry (METI) and NEDO*
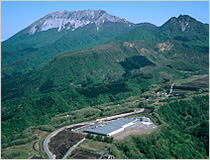
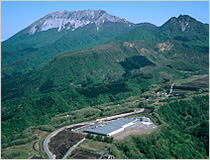
The New Energy Top 100 was established in order to spread the implementation of new energy considering factors such as regional characteristics throughout Japan. From among Japan’s 47 prefectures, the award is presented to innovative and pioneering projects that received high evaluation. This award recognized how the Okudaisen Buna no Mori Water Plant has a snow chamber that stores snowfall from the winter and then uses the snow for cooling machines in the production process, supplementing energy for air conditioning in the summer, etc. Furthermore, the award recognized how the plant achieved an annual reduction of approximately 400 tons for CO2 emissions through measures such as implementing an innovative latest heat storage system for efficient use of waste heat.
* New Energy and Industrial Technology Development Organization
March 19, 2009
Kanagawa Ayase Plant, Suntory Beverage Products Limited
Awards for Reduction in CO2 Emissions in the Food Industry: Minister of Agriculture, Forestry and Fisheries Award
Held by the Japan Research Institute, Limited
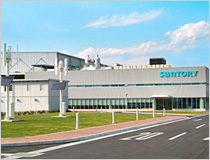
The Awards for Reduction in CO2 Emission in the Food Industry have been presented by the Japan Research Institute, Limited since 2009 in order to increase awareness toward reducing greenhouse gases and to disseminate information on outstanding cases within the food product industry.
Ever since its initial construction, the Kanagawa Ayase Plant has implemented a variety of energy-saving systems in order to reduce CO2. The plant has produced steady results since it began operation in 2007. The plant was highly recognized for achieving some of the largest reductions in CO2 intensity in the industry in 2008. This was made possible by conducting initiatives to reduce energy loss and achieve optimization throughout the entire plant.
December 8, 2008
Okudaisen Buna no Mori Water Plant, Suntory Tennensui Limited
5th Nikkei Monozukuri Award (2008) Held by Nikkei Inc.
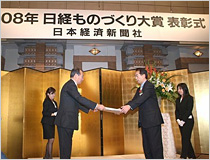
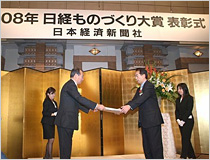
The Nikkei Monozukuri Award recognizes programs and systems implemented at outstanding factories and research centers involved in monozukuri (manufacturing), from among small, medium, and large corporations. Examples include special on-site measures and production systems for achieving production efficiency capable of competing with countries with low labor costs, skill inheritance programs which are implemented over a long-term perspective, and automation enabled by creating data for skilled labor.
The Okudaisen Buna no Mori Water Plant was recognized for comprehensive implementation of advanced environmental protection technology. Examples include sterilizing PET bottles without using chemical solutions, decreasing the weight of PET bottles, using natural energy provided by a snow chamber, and implementing a latest heat storage system that stores heat generated in the production process as energy that can be subsequently used as required.
September 29, 2008
Takasago Plant, Suntory Products Limited
Japan Greenery Research and Development Center Chairman's Award at the 27th National Convention for the Promotion of Factory Greening
Held by the Japan Greenery Research and Development Center
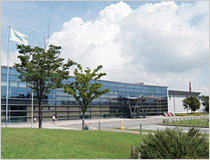
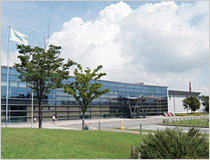
The National Convention for the Promotion of Factory Greening is held by the Japan Greenery Research and Development Center and was started in 1982 in order to recognize factories that have implemented outstanding initiatives for greening. The award is supported by various government agencies including the Ministry of Economy, Trade, and Industry (formerly the Ministry of International Trade and Industry).
From the time of its construction, the Takasago Plant has planted camphor trees, the official tree of Hyogo Prefecture, and Japanese pines, the official tree of Takasago City. In fiscal 2004, employees and children from a nearby kindergarten cooperated to plant chrysanthemum japonense, the official flower of Hyogo Prefecture. The flower bed uses fertilizer made from coffee grounds and green tea waste thrown away at Takasago Plant. The project combines caring for seedlings and recycling of waste products.